As someone who has always been fascinated by the inner workings of engines, I am a massive fan of GDI engines. GDI, which stands for Gasoline Direct Injection, is a mechanism that has revolutionized the way engines operate. “Gasoline Direct Injection,” or GDI, has revolutionized engine operation. GDI Engine Technology improves performance and fuel economy.
Originally developed for motorsport and high-performance vehicles, GDI technology has now been adopted widely across mainstream passenger vehicles. Automakers increasingly prefer GDI systems to meet strict global emission standards without compromising on power or driving dynamics. The high-pressure fuel delivery, when paired with precise timing, ensures that combustion occurs under optimal conditions, translating to cleaner and more efficient engine operation.
In India, automotive manufacturers such as Mahindra have adopted GDI technology in engines like the mHawk and mStallion, reflecting a growing industry trend. These engines not only support aggressive performance tuning but also offer smoother operation and better fuel management in real-world driving conditions.
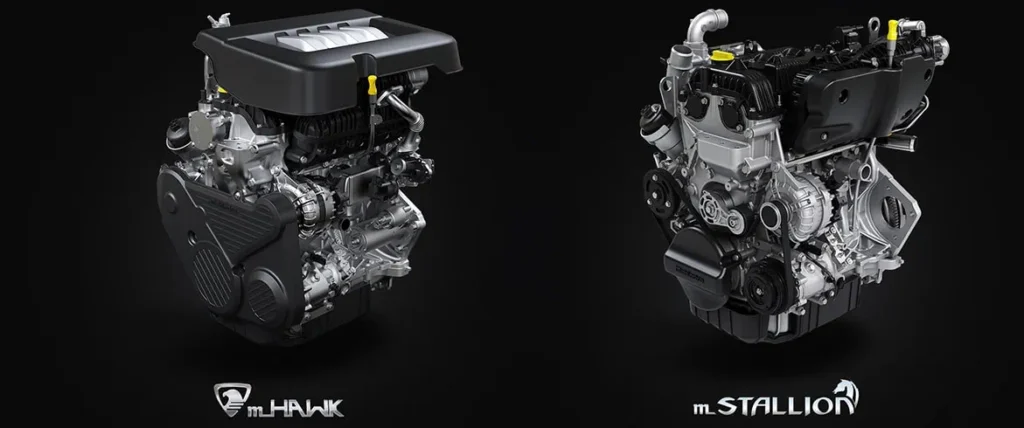
Picture Credits – Mahindra
GDI Engine
How Does the GDI Engine Work?
A GDI engine works by directly injecting fuel into the engine’s combustion chamber, bypassing the intake valves entirely. The process begins with fuel being drawn from the tank and pressurized by a high-pressure fuel pump. This pressurized fuel travels through a fuel rail and is then injected into the combustion chamber at precisely timed intervals.
Sensors installed throughout the engine monitor parameters such as throttle position, air intake volume, engine load, and temperature. This real-time data allows the Engine Control Unit (ECU) to determine the ideal amount and timing of fuel injection. Once the air and fuel mix in the combustion chamber, the spark plug ignites it, creating an explosion that powers the piston movement — and consequently, the vehicle.
Because the injection is so precise, the engine can operate using leaner air-fuel mixtures during cruising and richer mixtures during acceleration, improving both fuel economy and performance.
Pros of GDI Engines
- Improved Fuel Efficiency
By injecting fuel directly into the combustion chamber, GDI engines can maintain optimal air-fuel ratios under varying driving conditions. This leads to more complete combustion, reducing fuel consumption, especially during highway driving and low-load operations. - Enhanced Engine Power and Torque
Direct injection allows fuel to be delivered with better atomization and higher pressure, improving combustion characteristics. This results in more power and torque without increasing engine displacement, making GDI engines suitable for performance-oriented applications. - Lower Emissions
GDI systems can reduce the formation of certain pollutants, such as carbon monoxide (CO) and hydrocarbons (HC), due to better fuel burn. Advanced systems also reduce nitrogen oxides (NOx) and particulate matter (PM), supporting compliance with stringent emission norms. - Better Throttle Response
Because the engine can respond quickly to changes in fuel demand, throttle response is noticeably sharper. This improves acceleration and makes driving feel more dynamic and responsive. - Advanced Engine Tuning
GDI technology allows more precise tuning of the engine’s fuel map. Engineers can adjust injection timing, spray patterns, and fuel quantity to suit various driving conditions — such as cold starts, idling, or heavy loads — improving overall engine behavior.
Cons of GDI Engines
- Higher Manufacturing Costs
The high-pressure pumps, durable fuel rails, precision injectors, and robust ECU systems make GDI engines more expensive to manufacture than their PFI counterparts. This can slightly increase the vehicle’s price for the end consumer. - Increased Complexity and Maintenance
GDI engines are more mechanically and electronically complex. Their service and maintenance require specialized equipment and expertise, which may not be readily available at all workshops. - Carbon Build-Up on Intake Valves
Unlike PFI systems where fuel washes over the intake valves and keeps them clean, GDI systems bypass this step. Over time, carbon deposits can accumulate on the valves, leading to reduced airflow, poor performance, and the need for regular intake cleaning. - Fuel Sensitivity
The GDI system demands clean, high-quality fuel. Contaminated or low-grade fuel can damage injectors or disrupt combustion, reducing both performance and longevity. - Higher Combustion Temperatures
Direct injection increases the heat inside the combustion chamber, which may cause knocking or pre-ignition in some cases. Advanced knock sensors and engine tuning are necessary to manage these risks.
Engine Components of a GDI System
To achieve the precision and power benefits of GDI, several key components must work together seamlessly:
1. Fuel Injectors
GDI fuel injectors spray highly pressurized fuel directly into the combustion chamber. They must atomize the fuel into fine droplets for efficient combustion. There are typically two types:
- Solenoid Injectors: Operate using electromagnetic coils and are widely used in standard GDI systems.
- Piezo Injectors: Use piezoelectric crystals for faster and more precise fuel control, often found in premium or high-performance engines.
2. Fuel Pump
The system usually employs two pumps:
- Low-Pressure Pump: Draws fuel from the tank to the high-pressure pump.
- High-Pressure Pump: Driven by the engine (often via the camshaft), it compresses fuel to pressures of up to 2000+ psi before delivery to the injectors.
3. High-Pressure Fuel Rail
This rail distributes pressurized fuel evenly to each injector. It is typically made from stainless steel or reinforced alloys to withstand the immense pressure generated by the high-pressure pump.
4. Combustion Chamber
The chamber is designed for optimal mixing of air and fuel. Piston heads in GDI engines often have a bowl shape to facilitate mixture swirl and turbulence, which improves burn efficiency.
5. Engine Management System (EMS)
This is the electronic brain of the engine. The EMS controls injection timing, fuel quantity, ignition timing, and air-fuel ratio based on inputs from:
- Oxygen sensors
- Throttle position sensors
- Intake air temperature sensors
- Engine load sensors
The EMS ensures the engine runs smoothly under all driving conditions, from cold starts to high-speed cruising.
Conclusion
Gasoline Direct Injection engines have redefined how internal combustion engines deliver power, manage fuel, and control emissions. By enabling fuel to be injected directly into the combustion chamber, GDI engines enhance performance and fuel economy while also supporting stricter emission regulations. Their precision and responsiveness make them ideal for modern vehicles that demand both efficiency and dynamic driving experiences.
If you’re still unsure about the differences, you can check out our detailed comparison between PFI vs GDI engines here.
However, the benefits of GDI come with trade-offs: higher manufacturing costs, technical complexity, carbon build-up, and the need for high-quality fuel. Understanding these pros and cons, along with the working principles and components, can help consumers, mechanics, and enthusiasts appreciate the sophistication behind GDI engines.
As emission norms tighten and fuel economy becomes even more critical, GDI technology is likely to remain central to the future of internal combustion — especially when paired with hybrid systems or as part of transitionary strategies toward full electrification.
FAQs : GDI Engine
How does a GDI Engine work?
In these type of engines, fuel is injected directly into the combustion chamber at high pressure. This allows for a more precise control of the fuel-air mixture, resulting in better combustion efficiency, improved performance, and reduced emissions.
Why do GDI engines suffer from carbon buildup?
Unlike PFI engines, GDI engines don’t wash intake valves with fuel, since injection happens directly inside the cylinder. This can lead to carbon deposits on intake valves over time, which may affect engine performance and require periodic cleaning.
What is dual injection and how is it related to GDI?
Dual injection systems combine both GDI and PFI technologies. During certain conditions, the engine uses port injection to keep intake valves clean and reduce emissions, and switches to direct injection when more power or efficiency is needed. It’s a hybrid approach to overcome some of GDI’s limitations.
Can GDI engines run on regular fuel?
While most GDI engines are designed to run on regular unleaded fuel, some high-performance variants may recommend or require premium fuel for optimal performance and to prevent knocking. Always follow the manufacturer’s guidelines.
What types of vehicles commonly use GDI engines?
GDI technology is widely used in various types of vehicles, including passenger cars, trucks, and SUVs. It’s increasingly popular among manufacturers looking to improve fuel economy and meet stricter emissions standards.
Mechanical Engineer by Education. Writer by passion. Fortunate to combine passion and education. Huge F1 Addict and adventure head. You can find me in the mountains on the weekend.